Key Points When Choosing and Installing a Breeder LED Lighting System
This article aims to give the reader a general overview of LED lighting systems, how they work, and what differentiates the various systems available in the poultry industry. A knowledge of the basic principles and mechanics is important when considering which system best suites one's needs.
Some key questions to ask the potential suppler:
1. Efficiency - Lumen per Watt of the system.
2. Light uniformity – Dark spots and shadows result in floor eggs.
3. Lifespan – How many hours can I expect from the product?
4. Dimming flexibility – Can I dim from 80 Lux down to 2 Lux without flicker?
5. Ease of Installation - It is important to factor installation costs into your budget.
6. Operating costs- Based on installation cost, efficiency, maintenance, and lifespan
Some key lighting terms:
- Lumen (lm): Visible light emitted by a source.
- Lux (Lx) or foot candle (fc): Measurement of light at a distance.
- Colour Temperature - Kelvin (K): >5,000K are called cool colors (bluish white), neutral white is around 4,000K-5000K, while <3,000K are called warm colors (yellowish white through red). Warm colors 2700K (red spectrum) of light are best for pullet rearing and production, while broilers will perform equally over a range of colors as high as 5000K (blue /green spectrum).
- Lumen Per Watt: Visible light generated for every Watt of power consumed.
- Uniformity: Good uniformity means even levels of light with no shadows or dark spots.
- A Light-Emitting Diode (LED): A semiconductor light source that releases light when a current flows through it.
- LM70 Lifespan: The standard for determining LED lifespan is based on the hours it will take to depreciate to 70% of the initial lightoutput.
LED LUMINAIRE DESIGN ESSENTIALS
The LED
The LED or Light Emitting Diode may be the single most important component of the luminaire, but it is only one of many components required to make a product fit for full time operation in a poultry house. As with everything, you pay for what you get. More expensive brand name LEDs offer longer lifespans and higher efficiencies.
The Driver
LED chips generally operate on DC voltage. LED luminaires therefore require a driver which converts the incoming AC voltage to the required DC voltage. Drivers are either integrated inthe luminaire as typically found in LED bulbs or tubes or are external with a single driver powering multiple luminaires. When an LED luminaire fails, it is almost always a driver issue and not the LED chips. It therefore makes sense to use an external driver in a poultry house. Furthermore, external drivers powering multiple lights can be industrial grade units offering many benefits over internal drivers.
The Casing
Poultry houses are washed regularly using high pressure washing with chemical detergents. It is important to ensure that the product you choose has been designed for this environment. Products should have a minimum IP67 rating but ideally an IP69 which covers direct water jets.
The Dimmer
The dimmer is not a true luminaire part, but a major part of the system is the dimming functionality of the product. It is critical that the luminaire dims smoothly and without flicker from 0 to100%. Ensure that the dimmer has a 0 to 10V input to control from an environmental computer or PLC.
The Heatsink
An LEDs lifespan is directly influenced by its operating temperature. The cooler it operates the longer it lasts. For this reason, avoid LED globes in a “jam jar” or sealed cover to prevent overheating and premature failure. The heat sink size in relation to the power output is also very important. Always look for a large aluminium heat sink.
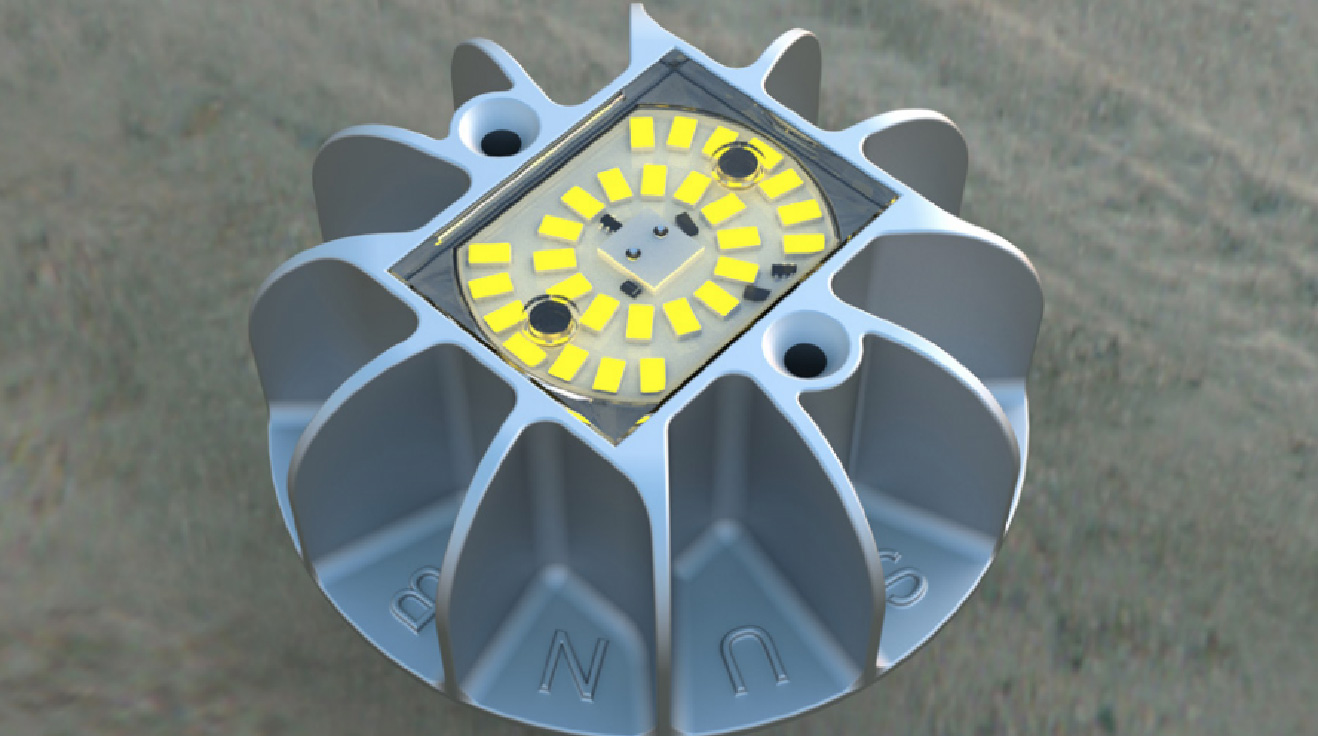
The LED’s lifespan is based on a lumen maintenance (LM) of LM70, which is the predicted number of hours it will take theLED to reach 70% of its original lumen output. The hotter an LED runs the faster its lumens depreciate. To determine the LM70, the manufactures test the chips over time, monitoring how the lumen output depreciates and then uses this data to project the expected lifespan. This data should be available and can be used as a purchase consideration. Below is an example of the results of a lumen depreciation test for an LED. A temperature probe is placed on the LED aluminum PC board to measure maximum case temperature, and a 2nd probe 20mm away from the heatsink to measure ambient temperature.
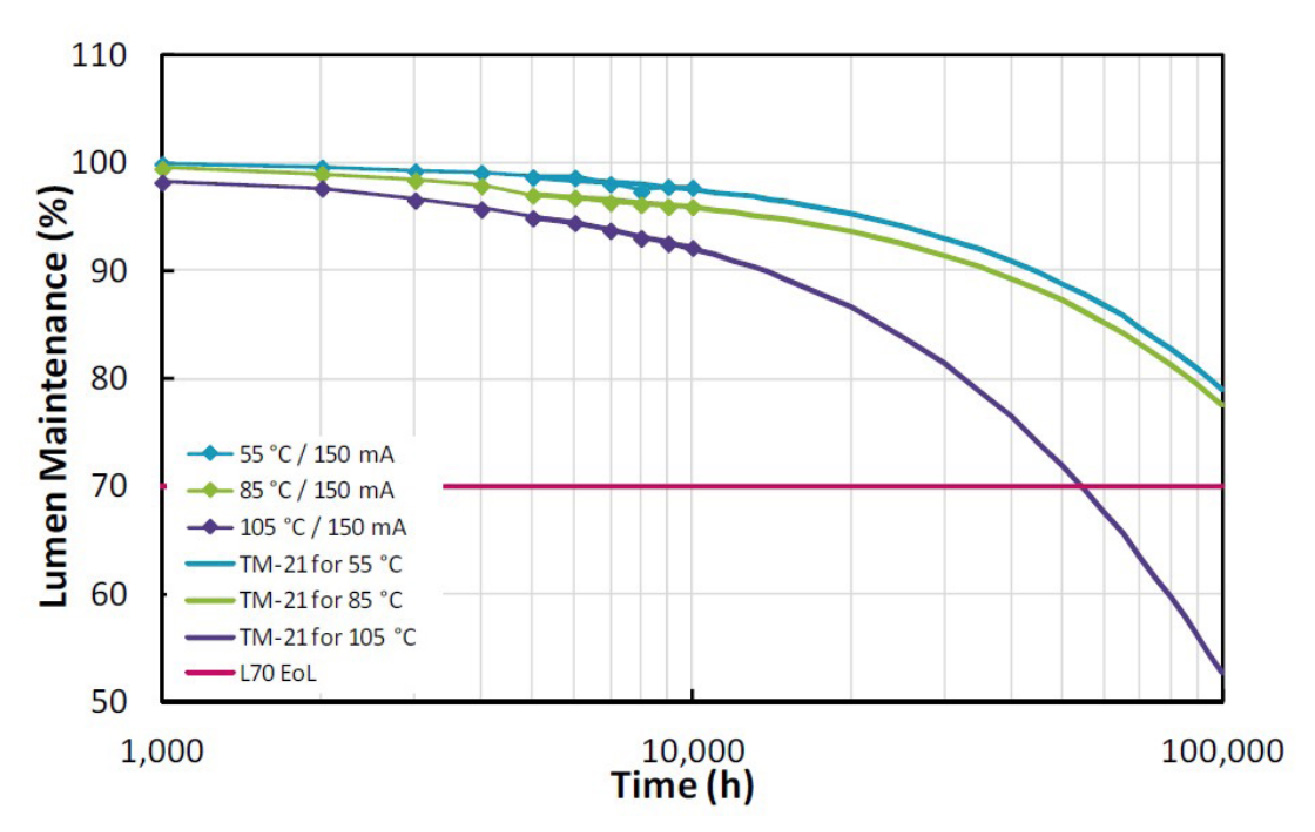
IMPORTANCE OF LIGHT UNIFORMITY AND DISTRIBUTION
When installing any lighting system for production houses, the primary goal is to always work towards eliminating any potential shadows. Where there are shadows there are floor eggs.
Manual Free-Standing Nest Box Systems
Designing lighting for nest box systems can be challenging. The best results are usually achieved when shadows are minimized, uniformity is maintained and light levels of around 80 Lux are achieved. A common mistake is to use fewer, more powerful lights to reach the required average Lux levels, but this results in more shadows caused by nesting boxes. For example, in a 12m wide manual nest house enough lux may be achieved by two rows of lights, but the result is too many shadows around the nesting boxes. This problem is solved by using 4 rows of LEDS with optimised spacing dramatically reducing shadows and thus flooreggs. The target uniformity in the nest free sections of the manual nest house is 80%.
The Community Nest and US Style System
Installations for these systems are usually easier and present minimal shadow issues. A community nest with a usual US style setup (1/3 scratch area and 2/3 slats) would typically have 4 rows of lights. The outer rows should be close to the side walls to illuminate this usually dark area with the two inner rows normally positioned above the step up to the slats to prevent a shadow in the step-up area. Some designers will prepare the lighting layout so that Lux levels diminish closer to the nest. This tends to draw the birds towards the darkness and the nest. Aim for 80% uniformity in the scratch area, which is not always possible if light diminishes towards the nests.
An experienced agricultural LED supplier will require house dimensions (length, width, and roof height) and the layouts of nest boxes and feed hoppers. Using this information, they will create a simulation model that is used to design a light layout ith minimal shadows and an even distribution of light at the required Lux levels (see examples below).
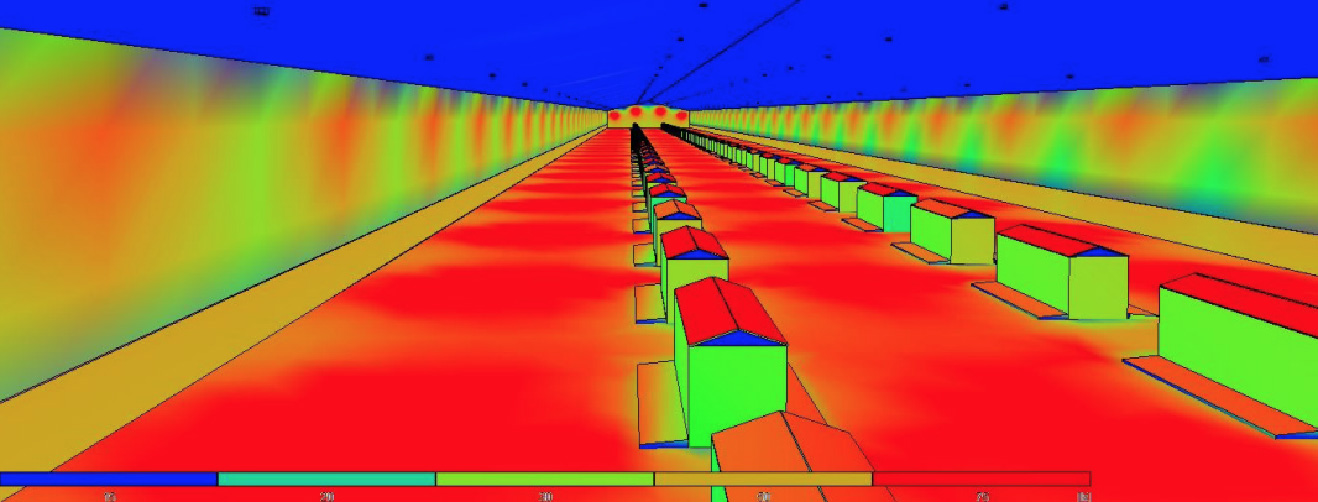
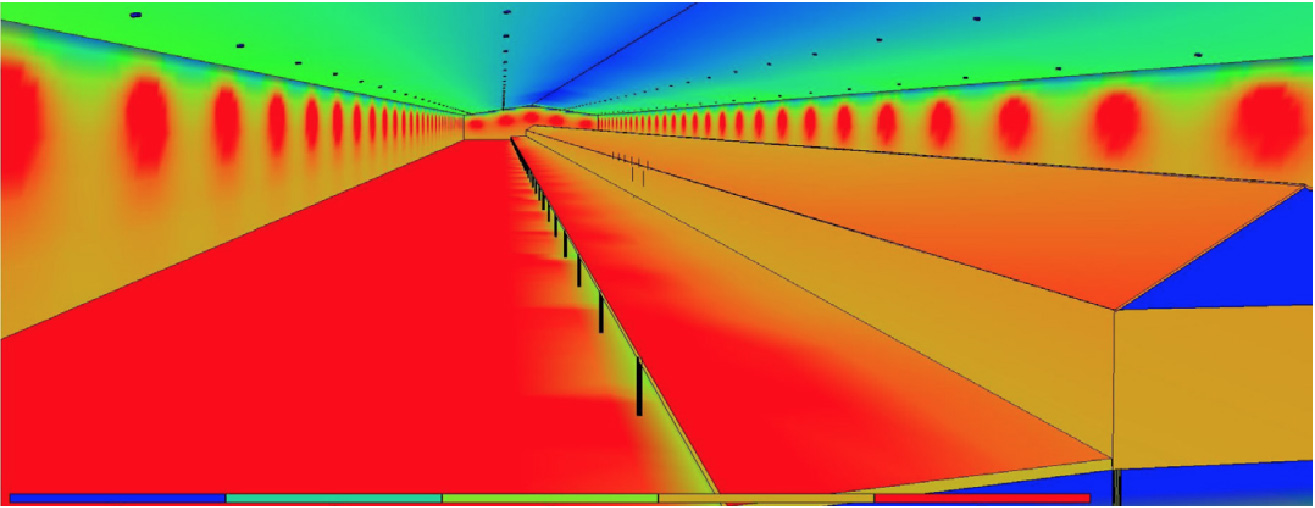
INTERNAL VERSUS EXTERNAL DRIVERS
LED chips operate on a low voltage DC current. The grid supplies 110/220V AC current which is commonly converted into either 12, 24, 36 or 48V DC by a LED driver. Drivers (transformers) regulate power to a single LED or to a string of LEDs. Direct AC (alternating current) LEDs are now available but are not recommended for poultry lighting. These chips will go dark every mains half-cycle or 1/100th of a second in a 50Hz mains system, when the voltage is at or near to 0V. This may appear as flickering to the birds and can cause stress.
Integrated drivers are incorporated into a single LED luminaire whereas external drivers can power multiple LED luminaires. Integrated drivers offer limited protection against shortcircuits, over current, over voltage and electro-magnetic interference (EMI) caused by switching electric motors (the modern poultry house has many electric motors). Most LED bulb failures are due to integrated driver failure and not the LEDs themselves.
Leading poultry lighting manufacturers have all seen the benefits of using external drivers. It is important to note the following characteristics and benefits:
- Voltage drop - when choosing a low voltage system, beaware that they are prone to a voltage drop over the lengthof the house. The lower the voltage the more susceptible thesystem. A 12V system is particularly prone to voltage drops,which could cause the front of the house to be brighter than the rear. A 48V system is 3 times less susceptible compared to a 12V system. A voltage drop can be mitigated with the correct gauge wire. A reputable supplier will always take voltage drop into account when preparing wiring diagrams and installation instructions.
- Safety – Voltage below 50V is considered safe and does not require a certificate of conformity for installation on theDC side of the installation. Low voltage systems have an external driver mounted in the house’s control room providing low voltage power to the entire circuit eliminating the risk of electrical shock.
- Washing and disinfection - AC supply circuits, unlike lowvoltage systems, are susceptible to short circuits caused by water in a conduit after a wash cycle, often resulting in the loss of all the LED bulbs on a circuit.
- Stability - The use of an external driver (instead of the small integrated units) means that a more industrial type unit can be used to power many lights. The larger external drivers have far superior protection against voltage spikes and are not impacted by EMI.
- Power-factor correction (PFC) - PFC increases the power factor of a load, improving efficiency for the distribution system to which it is attached. It is important to select a system that is power factor corrected to ensure maximum efficiency.
- Dimming - By having an external driver, the dimmer can be positioned between the driver and the LEDs thereby eliminating compatibility issues associated with “dimming” integrated drivers.
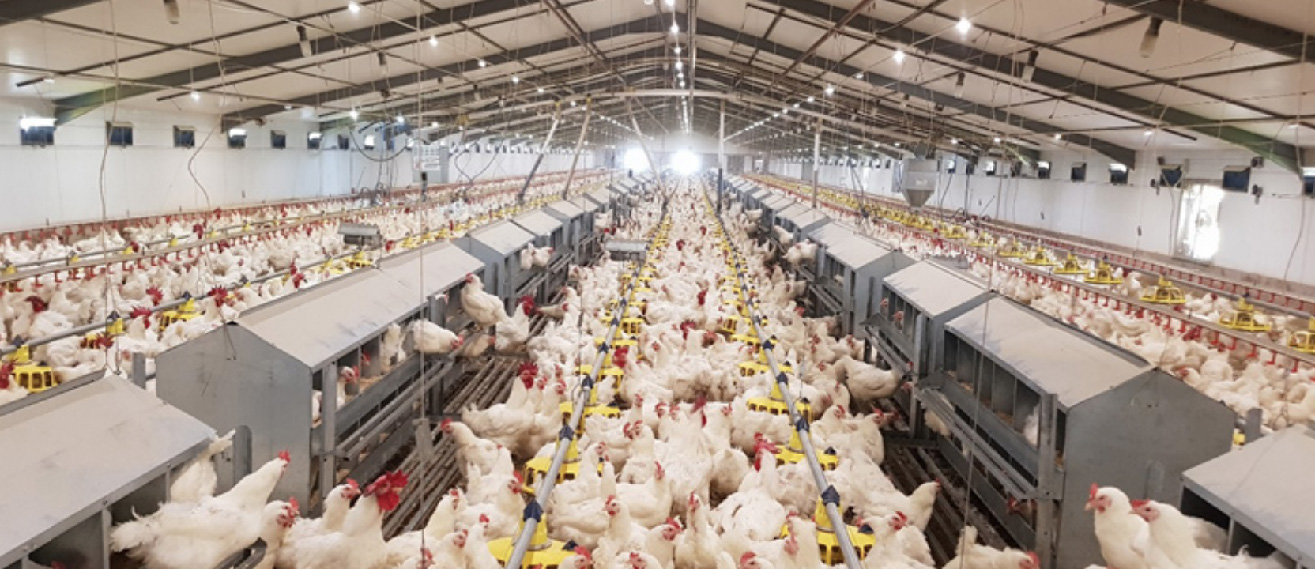
THE IMPORTANCE OF DIMMING
A breeder house could have as many as 200 lights, all of which need to dim uniformly without flickering. To decrease to very low Lux levels (80 Lux down to 2 Lux), the system needs to be able to dim down to a minimum of 2.5%. For true simulation of dusk to dawn, the system must be able to dim down to 0%. Many LED systems sold to the agricultural industry will claim to dim down to 0%, but often, this is not the case. In reality, many will turn off at around 5 to 10%.
The two common methods for dimming LEDs are Constant Current Reduction (also known as Analog Dimming) and Pulse Width Modulation (PWM).
Analogue Dimming (constant current reduction)
Analogue dimming or (constant current reduction) is suited for bulbs or tubes with integrated drivers supplied with high voltage AC. In these systems, the dimmer chokes the current to the integrated drivers which in turn chokes the current to the LEDs. This form of dimming is prone to compatibility issues especially where you have many lights on a single dimmer. Minimum dimming levels are limited to between 5 and 10%. Moreover, some units switch on or off before other units at low levels making Dusk to Dawn dimming problematic.
Pulse Width Modulation (PWM)
PWM is a very common method of dimming LED lights that works by very rapidly turning them on and off (pulsing) for periods that visually appear as a steady dimmed light. The brightness level is adjusted by adjusting the percentage of the time the lights are on (100%) to the time they are off (0%).The dimmer is situated between the driver and the LEDs. The frequency commonly used is greater than 700Hz which is well beyond the flicker threshold a bird (+-100Hz) can detect.
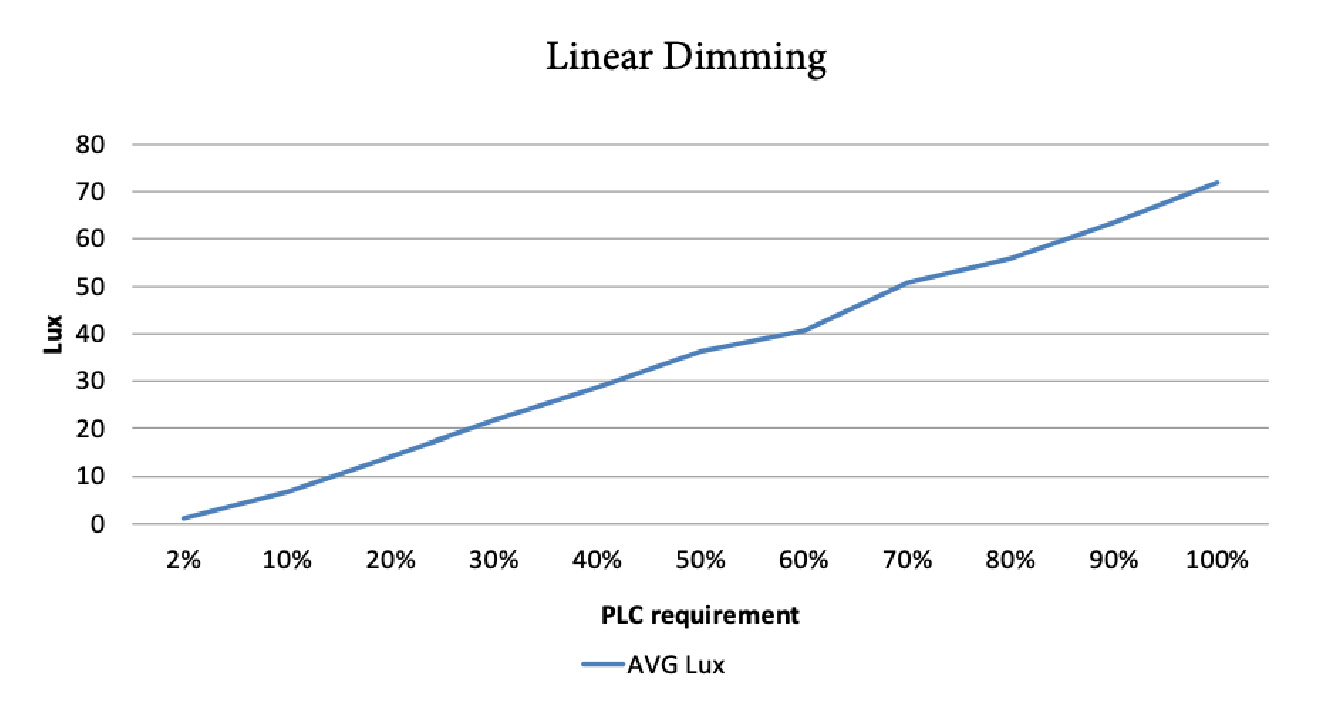
Conclusion:
Use the right tool for the job. Get your lighting done right from the start by speaking to a company that specializes in poultry lighting. Opt for an Aluminum heat sink. Stick to the basics- warm white for breeders, the more uniform the better, no shadows, 80 Lux target intensity and smooth dimming with no flicker.
Authors note: Special thanks to Philip Malherbe at Sunbird Poultry Lighting for the images and technical help
View the original article here